RUTILE - LOW ALLOY - HIGH EFFICIENCY HARDFACING ELECTRODE FOR BALANCED RESISTANCE TO ABRASION AND IMPACT LOADING
HV-600
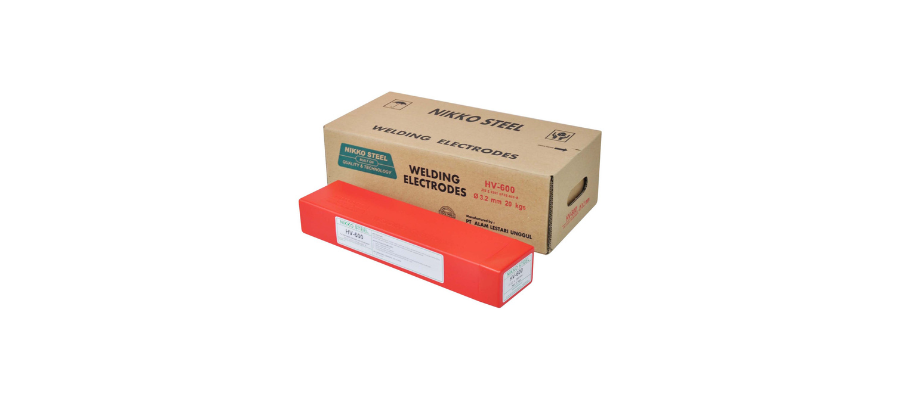
CLASSIFICATION
AWS A5.13 EFe3 | DIN 8555 E6-UM-60-GP | JIS Z 3251 DF3B – 600R
PRODUCT DESCRIPTION
The design emphasis of the alloyed weld metal ensures the desired hardness level to the specification is readily achieved as is the deposits maximum resistance to impact loading combined with medium resistance to abrasion. The flux contains the appropriate alloying elements plus iron powder addition and is extruded onto a ferritic wire with a balance of silicates that ensures both coating strength and resistance to moisture absorption.
WELDING FEATURES OF THE ELECTRODE
The electrode is suitable for both AC and DC and is used to best advantage in the flat and HV positions. The arc is smooth and stable weld beads are evenly rippled, of bright appearance and the slag readily detachable. The weld deposit is highly crack resistant under normal circumstances, but on high carbon cast steels or restrained sections of mild steel, a pre-heat of 150 °C should be used.
APPLICATIONS AND MATERIALS TO BE WELDED
On high carbon steels HV-250B should be used as a buffer layer.
The weld deposit has good resistance to abrasion, under normal circumstances
is crack free, and will withstand a reasonable amount of impact loading.
Used to particular advantage for : bulldozer blades, crusher jaws, bucket lips
and teeth involved in earth moving and mineral crushing. Where the main wear
is abrasion, but with some impact resulting from rocks and compacted minerals.
Under normal circumstances the weld metal is non-machinable.
WELDING AMPERAGE AC and DC
OTHER DATA
Electrodes that have become damp should be re-dried at 150ºC for 1 hour.