LIME RUTILE FLUX COATED ELECTRODE WITH VERY LOW LEVELS OF SILICIOUS MINERALS THAT DEPOSITS A NOMINAL 16Cr–8Ni– 2Mo WELD METAL TO RESIST THERMAL EMBRITTLEMENT
NS-16.8.2
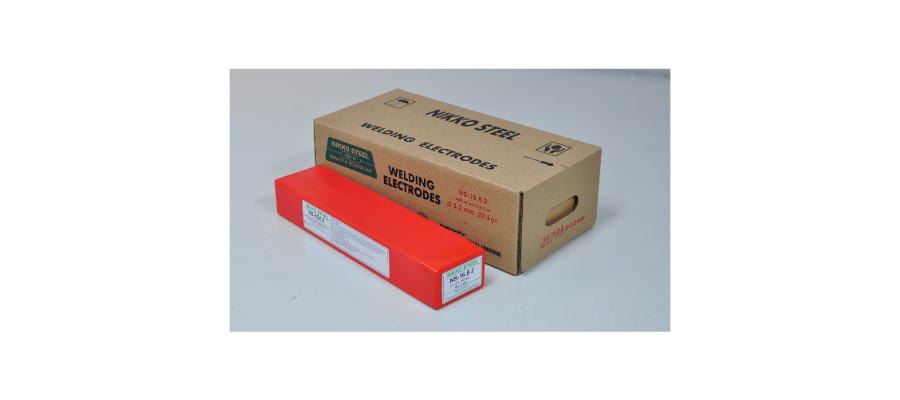
CLASSIFICATION
AWS A5.4 E16-8-2-16 | EN ISO 3581-A E 16 8 2 R
PRODUCT DESCRIPTION
Manufactured on a near matching alloy core wire, the rutile low silicious flux has a significant level of chemically basic chemicals that ensures a high purity weld metal with a refined microstructure. The flux is extruded on to the core wire using a blend of silicates that ensures both coating strength and a coating resistant to subsequent moisture absorption.
WELDING FEATURES OF THE ELECTRODE
The electrode performs best on DC+ but may be used AC. The arc is stable but should be used with a short arc technique rather than contact welding. The medium viscous slag is readily detachable even in deep v-grooves. Vertical up welding is possible with 3.2mm diameter electrodes. Fillet welds have a convex profile
APPLICATIONS AND MATERIALS TO BE WELDED
Designed for welding 316, 316H, 321, 321H, 347 and 347H austenitic stainless steels operates at temperatures between 450 - 800ºC. The Cr and Ni levels of the weld metal are balanced and below that of standard 316L levels to ensure low delta ferrite, eg: FN 2 to 8, which ensures resistance to thermal embrittlement. Applications occur in power stations, petro-chemical industries, for welding pipes, superheater headers and turbine components.
WELDING AMPERAGE AC and DC
OTHER DATA
Electrodes that have become damp should be re-dried at 180oC for 1 hour