LOW HYDROGEN - LOW ALLOY - HIGH EFFICIENCY HARDFACING ELECTRODE FOR BALANCED RESISTANCE TO ABRASION AND IMPACT LOADING
HV-450B
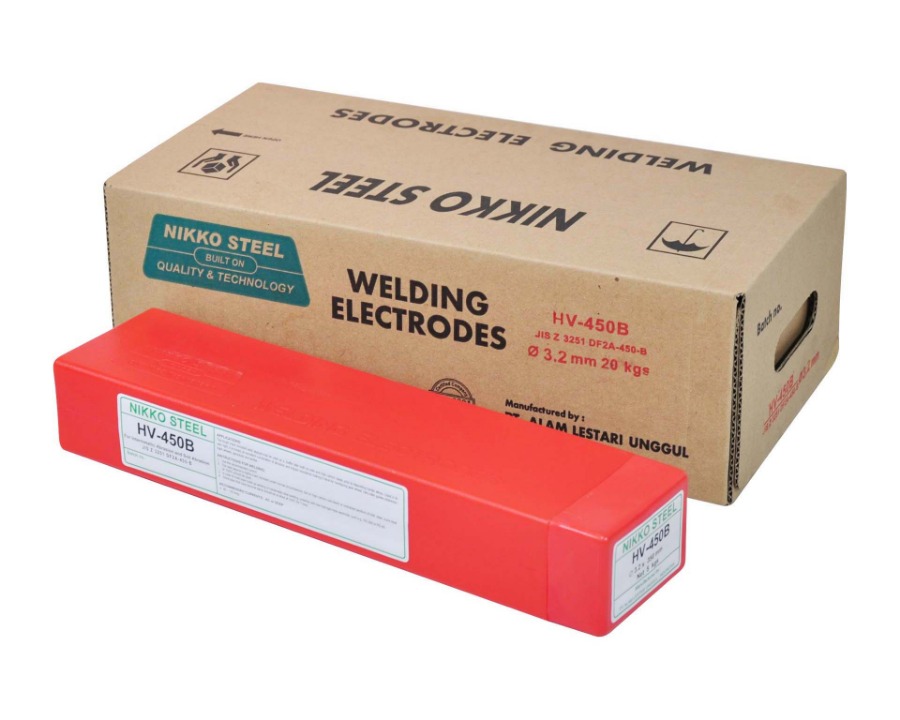
CLASSIFICATION
AWS A5.13 EFe2 | DIN 8555 E1-UM-45-GP | JIS Z 3251 DF2A - 450B
PRODUCT DESCRIPTION
The design emphasis of the chemically basic flux is engineered to ensure that the weld metal hardness levels demanded by the specification are fully met without detracting from the toughness levels associated with this class of alloy. The basic flux containing the appropriate alloying elements and a balanced addition of iron powder is extruded onto a high purity ferritic core wire using a balance of silicates that ensures both coating strength and resistance to moisture absorption.
WELDING FEATURES OF THE ELECTRODE
The electrode is suitable for both AC and DC and may be used in all positions except vertical down. Arc stability is good as is slag detachability. Weld seams are smooth, evenly rippled and slightly convex in shape. The metal recovery of the electrode is some 120% with respect to weight of the core wire.
APPLICATIONS AND MATERIALS TO BE WELDED
The tough crack resistant weld deposit may be used as a buffer layer both on mild and high carbon steels prior to depositing harder alloys. Used in its own right, it provides an excellent combination of abrasion and impact resistance making it ideal for hardfacing gear wheels, rails, roller guides, slideways, track wheels, sprockets and similar. Machining is not possible but may be profile ground
WELDING AMPERAGE AC and DC
OTHER DATA
Electrodes that have become damp should be re-dried at 150ºC for 1 hour.