BASIC HARDFACING ELECTRODE DEPOSITING WELD METAL HIGH IN CHROME CARBIDE PROVIDING EXCELLENT RESISTANCE TO ABRASION
HV-950
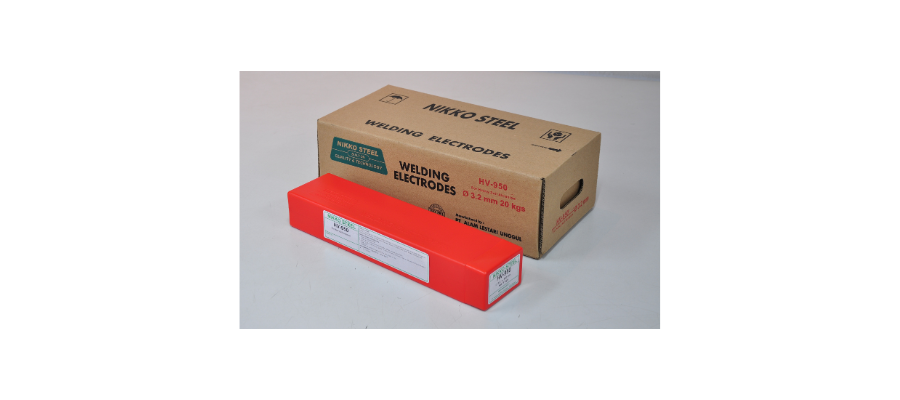
PRODUCT DESCRIPTION
The design emphasis of the chemically basic flux is engineered to ensure that the
weld metal hardness levels demanded by the specification are fully met without
detracting from the toughness levels associated with this class of alloy.
The basic flux containing the appropriate alloying elements and a balanced
addition of iron powder is extruded onto a high purity ferritic core wire using a
balance of silicates that ensures both coating strength and resistance to moisture
absorption.
WELDING FEATURES OF THE ELECTRODE
The electrode welds with a smooth stable arc and easily strikes and re-strikes. Weld appearance is bright, almost of polished appearance, smoothly contoured and slag detachability is excellent. The metal recovery is some 170% with respect to core wire weights, thus reducing welding time. The weld deposits are non-machinable.
APPLICATIONS AND MATERIALS TO BE WELDED
Suitable for surfacing a wide range of steels including 13Mn types. Because thermal contractional stresses will cause stress relieving cross-cracking, buildups should be limited to 3 layers, preferably two when restraint is high. The deposit has excellent resistance to abrasion against minerals, sand and sludges which leads to its extensive use in the earth moving, cement, dredging and steel industries. For build-ups on carbon and low alloy steels or 13Mn steel, NS-307 should be used as a buffer layer.
WELDING AMPERAGE AC and DC
OTHER DATA
Electrodes that have become damp should be re-dried at 150ºC for 1 hour.