A CHEMICALLY BASIC FLUX COATED ELECTRODE THAT DEPOSITS A NIOBIUM STABILISED WELD METAL CONTAINING A NOMINAL 35Cr-45Ni RESISTANT TO THERMAL FATIGUE UP TO 1150ºC
NCNb-35.45
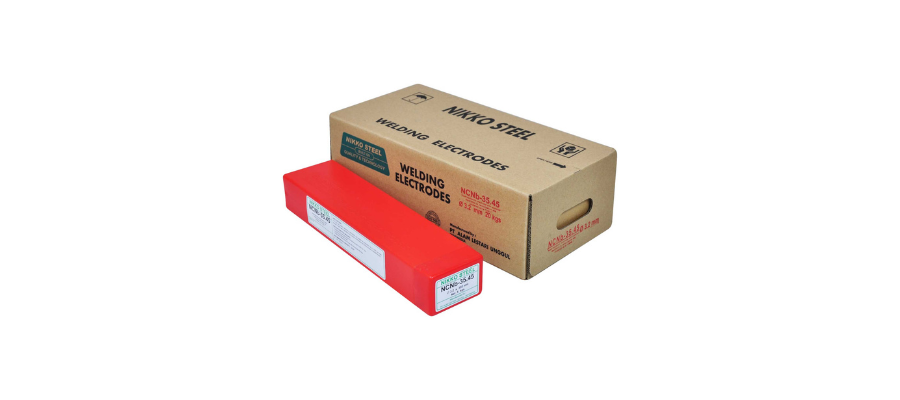
CLASSIFICATION
No Specification
Exists For This Electrode, But It May Be Compositionally Coded As 35.45.HNb B
PRODUCT DESCRIPTION
Manufactured on a high purity Cr-Ni wire, the chemically basic flux provides high resistance to microfissuring when welding thick sections and ensures low levels of non-metallic inclusions. The flux is extruded on to the core wire using a blend of silicates that ensures both coating strength and a coating resistant to subsequent moisture absorption
WELDING FEATURES OF THE ELECTRODE
Suitable for use on DC+ only, the arc is stable and directional but strike and restrikes should be made with the back-step technique. The weld beads are bright with fillet welds having a convex profile. Slag detachability is good even in thick butt welds. Positional welding is best undertaken with 3.2mm and smaller diameters. Metal recovery is some 130% with respect to weight of core wire.
APPLICATIONS AND MATERIALS TO BE WELDED
This Alloy has superior resistance to carburisation and oxidation than those based on 25.35.HNb at temperatures up to 1150ºC but creep strength is slightly lower. Applications occur mainly in the Petro Chemical Industry. Proprietary alloys include Lloyds T80 and T75 Ma (LBA). Paralloy it 46M (Doncaster Paralloy).
WELDING AMPERAGE AC and DC
OTHER DATA
Electrodes that have become damp should be re-dried at 150oC for 1 hour.