COBALT BASED ALLOY ELECTRODE FOR SURFACING ON CARBON STEELS, LOW ALLOY STEELS, STAINLESS STEELS AND NICKEL BASED ALLOYS
NS ECo-6
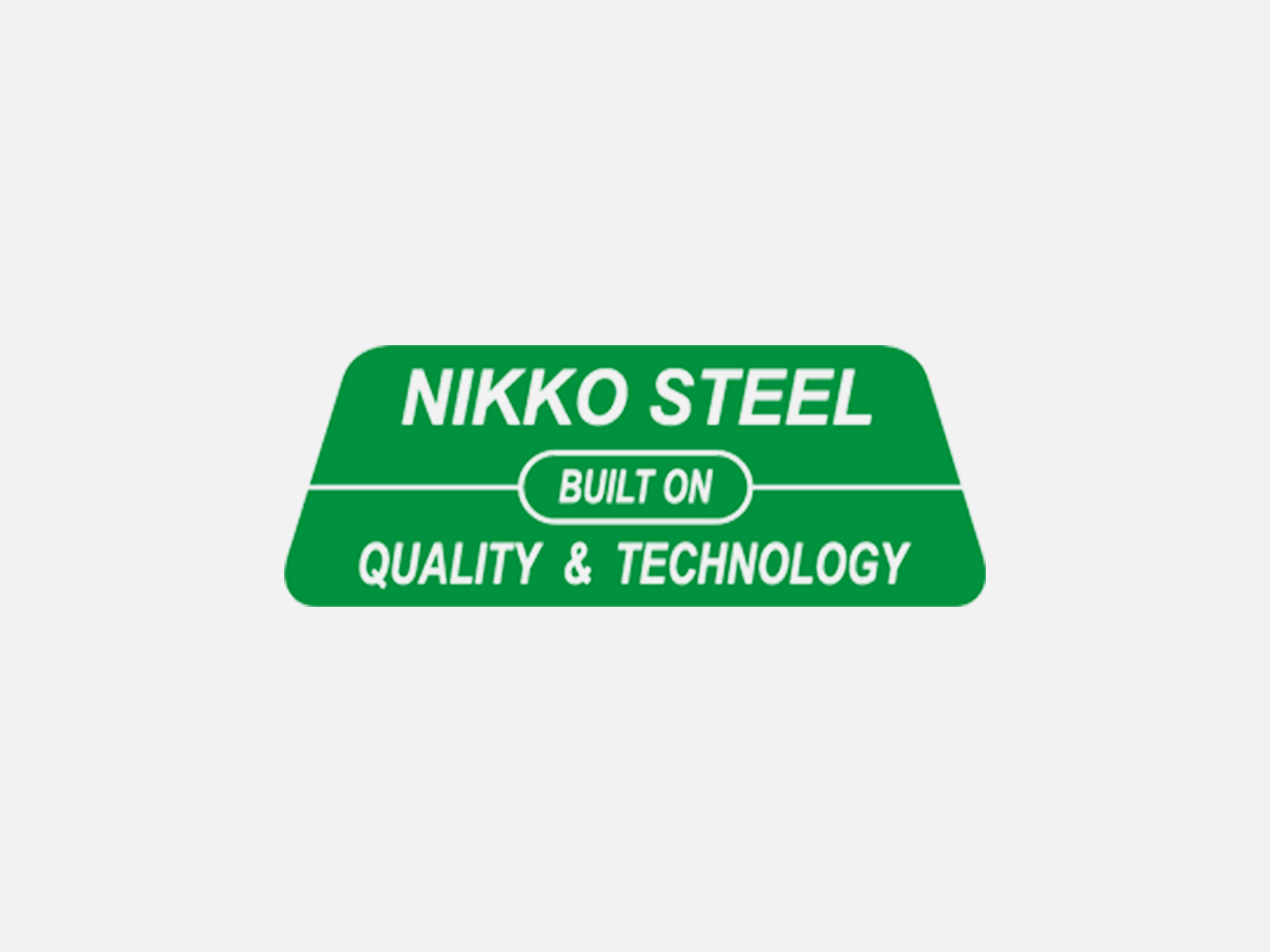
CLASSIFICATION
AWS A5.13 ECoCr-A | JIS Z 3251 DCoCrC-450BR
PRODUCT DESCRIPTION
A metallurgically balanced rutile basic flux with controlled additions of high purity amphoteric and acid minerals to adjust molten slag to that compatible of cobalt based alloys. The flux in concentrically extruded onto a fully alloyed core wire using a blend of silicates that ensures both coating strength and resistance to moisture absorption.
WELDING FEATURES OF THE ELECTRODE
The electrode is used to best advantage on DC+ but is also very stable on AC. Slag detachability is good even when using high preheat. Weld beads are bright and smooth-slightly convex in shape. This convex shape combined with preheat of 100°- 300° C provides maximum resistance to solidification cracking on multipass welds and when restraint is high.
APPLICATIONS AND MATERIALS TO BE WELDED
The alloys ability to withstand thermal shock combined with good resistance to abrasion, erosion, corrosion, oxidation and compressional stresses between 20°and 1000°C have led to its extensive usage in the following industries: Steel, cement, marine, petrochemical and power generating.
Applications include valves, valve seats, hot shear, blades, punches, dies, hot steel, handling components, catalystic crackers, cutting knives.
WELDING AMPERAGE AC and DC
OTHER DATA
Electrodes that have become damp should be re-dried at 150ºC for 1 hour.