A Self Shielding Flux Cored Wire With A Fully Austenitic Deposit For Buffer Layer Of Wear Surfacing And Joining Of Dissimilar Steels
NSF-307
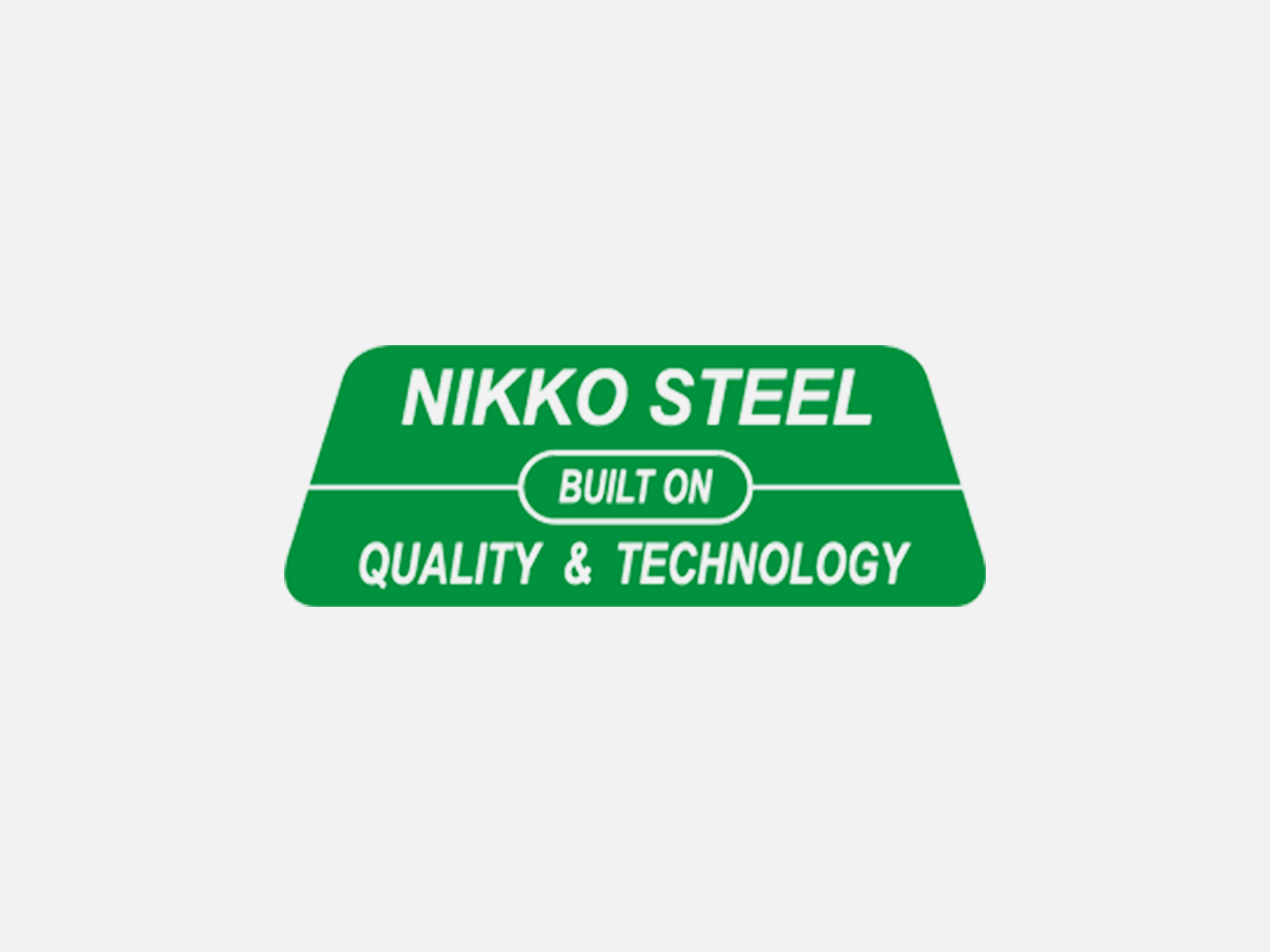
CLASSIFICATION
AWS A5.22 E307T1-3
PRODUCT DESCRIPTION
A tight seamed roll-drawn tubular wire containing an evenly distributed mixture of alloying elements, deoxidants and chemically basic minerals. The formulation of the wire is such that it eliminates the need for external shielding gas. The as deposited weld metal is ductile but tough and under conditions of impact loading rapidly work hardens.
WELDING FEATURES OF THE ELECTRODE
Suitable for use on DC+ only, the strong forceful arc is readily controllable and the high silicon content of the alloy lowers the surface tension of the molten weld pool, thus allowing ease of weaving and thus minimal dilution. Weld beads are bright and smooth and free from porosity. The slag volume is minimal and metal recovery is about 90% with respect to weight of the consumable.
APPLICATIONS AND MATERIALS TO BE WELDED
Suitable for the repair welding of high carbon problem steels and welding such steels to conventional stainless steels. However, its main field of application is for re-building 12 to 14% manganese steels subject to frictional and impact loading. However, as its rate of work hardening is slower than that of 12 to 14% manganese steels when heavy rolling loads are involved, it should be used as a buffer layer only, e.g. carbon steel mill rolls and similar, should be completed with FC-14Mn. Also suitable for multi layer deposits on 13Mn steel components subject to impact loading and moderate abrasion and in slurries give superior corrosion resistance to 12 to 14% manganese steels
WELDING AMPERAGE AC and DC
OTHER DATA
1. For carbon steel, pre-heat as necessary and interpass controlled to some 50oC above pre-heat temperatures
2. For 12 - 14% manganese steels, use minimum pre-heat and control interpass temperature to 150oC max.
3. Wires that have become damp should be re-dried at 120oC for 1 hour.