FOR WELDING OR REPAIRING HIGH-ALLOY HEAT AND CORROSION-RESISTANT STEEL CASTINGS WHICH OPERATING UP TO 1000ºC
NSN-310H
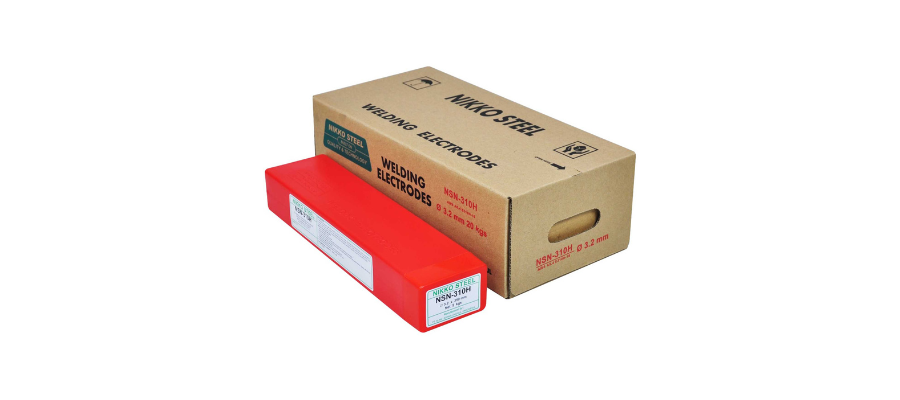
CLASSIFICATION
AWS A5.4 E310H-16 | EN ISO 3581-A E 25 20 H R
PRODUCT DESCRIPTION
A unique rutile based flux formulated with very low levels of acid and amphoteric minerals combined with small alloy additions to compensate for arc losses. The flux is concentrically extruded onto a fully alloyed core wire and bound by a blend of silicates that assures both coating strength and resistance to subsequent moisture absorption.
WELDING FEATURES OF THE ELECTRODE
The electrode is used to best advantage on DC+ but is also stable on AC. Weld beads are smooth and slag detachability is good. Because weld metal silicon is low by design to reduce solidification cracking (a feature common to all ferrite free austenitic alloys), the weld profile is more u-convex than normal.
APPLICATIONS AND MATERIALS TO BE WELDED
The electrode is designed to weld HK40 operating at 1000ºC as used in steam, chemical and petro-chemical plants. Also for components in the cement, ceramic and steel industries. Other materials to be welding include : ASTM A351, A608 Grade HK40. A297 Grade HK. BS 3100 Grade 310 C40, 1504 Grade 310C40. Proprietary alloys include: H20 Paralloy Thermalloy 47 (Duralloy) Lloyds T47 (LBA). HR6 (Cronite)
WELDING AMPERAGE AC and DC
OTHER DATA
Electrodes that have become damp should be re-dried at 180oC for 1 hour