Fully Martensitic 13%Chrome-Steel Electrodes For Surfacing Of Carbon Steels To Resist Corrosion, Erosion, Or Abrasion
NSN-410H
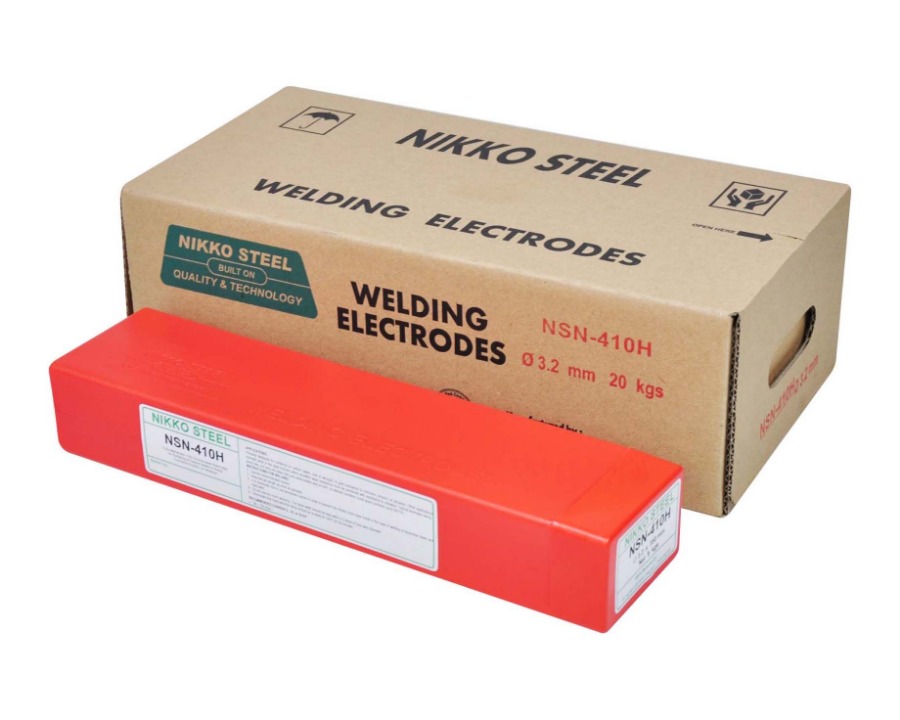
CLASSIFICATION
AWS A5.4 E410-26 (modified)
PRODUCT DESCRIPTION
A modified 410 electrode with higher carbon levels which is used only for surfacing not for joining. This electrode use special rutile based flux with a positive ratio of chemically basic minerals to acid minerals that contains all the major alloying elements which is extruded onto a high purity ferritic wire. The use of balanced silicates ensures both strength of coating and resistance to moisture absorption.
WELDING FEATURES OF THE ELECTRODE
The arc stability is excellent on both AC and DC+ as is the electrodes ability for initial arc strike and re-striking. Spatter is minimal and the slag is readily detachable leaving smooth evenly rippled seams of pleasing appearance. Metal recovery is some 130% with respect to weight of the core wire. Pre-heat and interpass temperature should be 200 oC max. As welded would only gives 2% elongation, thus the need for post weld heat treatment (730 – 760 oC / 1h, furnace cool to 315 oC at 60 oC/h max., air cool to room temperature)
APPLICATIONS AND MATERIALS TO BE WELDED
Primarily designed for surfacing on carbon steels, cast or wrought, to give resistance to corrosion, erosion, or abrasion. Other applications normally arise in the steel industry when excellent wear resistance must be combined with resistance to oxidation. Typical examples being : pinch rolls, hot strip mill table rolls, cast valve bodies and so forth. As welded condition could gives hardness up to 550 HV.
WELDING AMPERAGE AC and DC
OTHER DATA
Electrodes that have become damp should be re-dried at 120oC for 30 minutes.