Low Hydrogen Electrode For Welding 1.25cr-0.5mo Steels Subjected To Service At Elevated Temperatures Up To 550 ºC
RD-16B
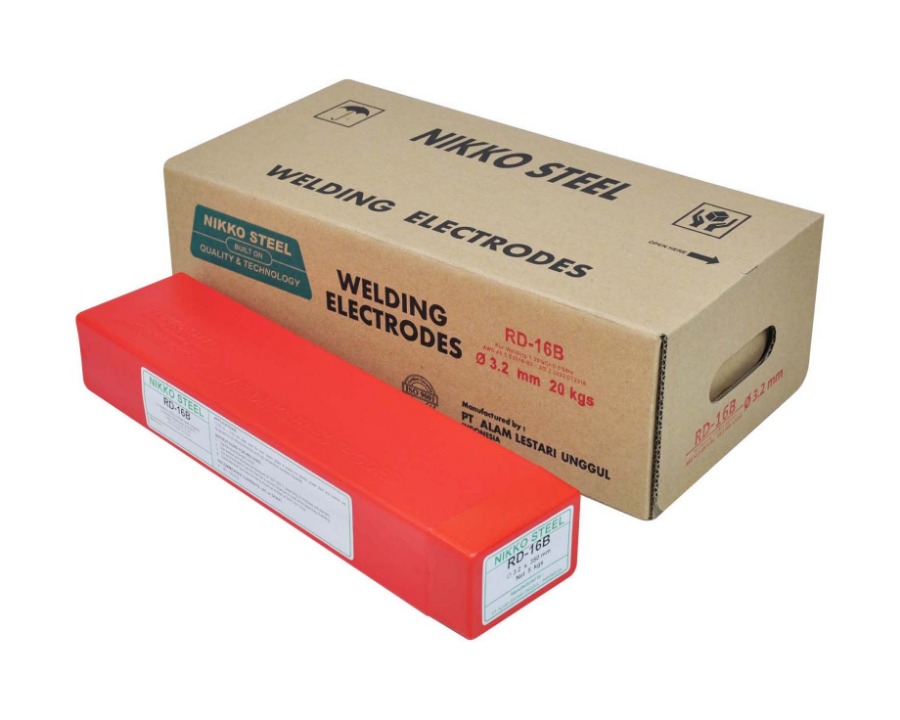
SPECIFICATION
AWS A5.5 | EN ISO 3580-A | JIS Z 3223
CLASSIFICATION
E8016-B2 | E CrMo1 B | DT2316
PRODUCT DESCRIPTION
The design emphasis of the chemically basic flux is engineered to ensure the optimum weld metal properties demanded by the specification are fully met. The basic flux containing the appropriate alloying elements but minimal iron powder, is extruded onto a high purity ferritic core wire and bound with a blend of silicates that ensure both coating strength and a coating resistant to subsequent moisture absorption
WELDING FEATURES OF THE ELECTRODE
The chemical nature of the flux together with its controlled coating factor allows the electrode to be used at relatively low amps. This factor together with the fairly fluid but quick freezing slag facilitate vertical up welding including controlled penetration root runs. Overall the arc is very stable, slag detachability is good, fillet welds are slightly convex and metal recovery is some 98% with respect to weight of the core wire.
APPLICATIONS AND MATERIALS TO BE WELDED
PLATES TO : BS1501: Part 2 Grades 620 and 621 ASTM A387 (pressure vessels) Grades 11 and 12. FORGINGS TO : BS 1503 Grade 620 and 621 CASTINGS TO : BS 1504 Grade 620 and BS3100 Grade B2. ASTM A217 WC6, WC11 PIPES TO : BS3604 Grades 620 and 621. ASTM A335 Grades P11 and P12. ASTM A155 Grades ½Cr and 1¼Cr. A182F11 and F12. TUBES TO : BS3059 Grade 620, ASTM A199, A200 & A213 Grades T11 & T12. HEAT AND CREEP RESISTANCE UP TO 550ºC WHEN WELDING. PRE-HEAT & INTERPASS TEMPERATURES 160ºC MIN AND UP TO 250ºC FOR THICK SECTIONS
WELDING AMPERAGE AC and DC
OTHER DATA
Electrodes that have become damp should be re-dried at 150oC for 1 hour