For Joining Difficult To Weld High Carbon Steels And Dissimilar Metal Combination When No Exact Specification Of The Base Metal Exists
NSK-312
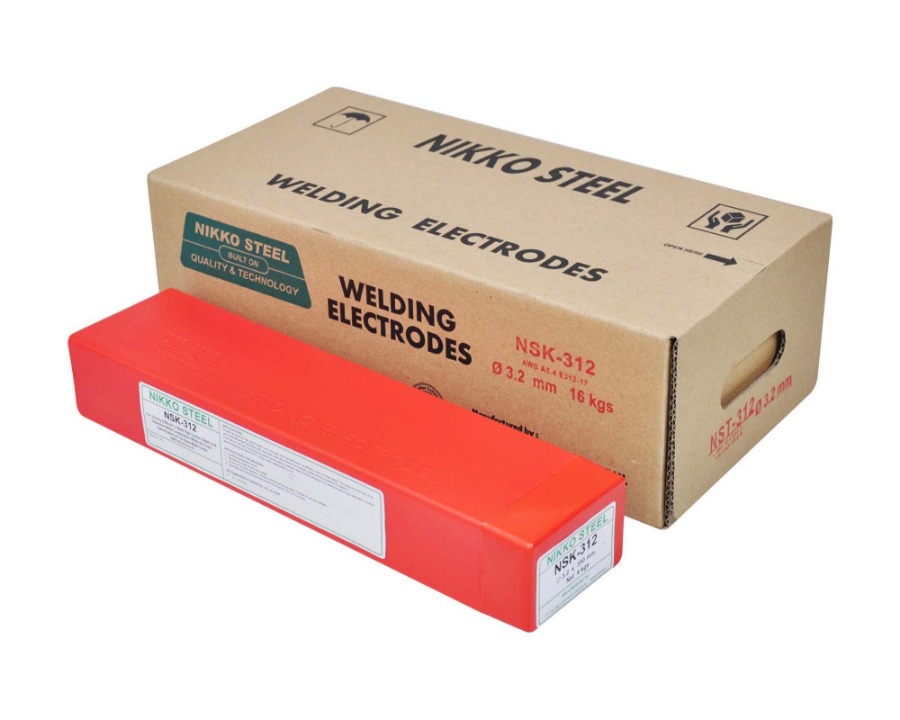
CLASSIFICATION
AWS A5.4 E312-17 | EN ISO 3581-A E 29 9 R
PRODUCT DESCRIPTION
A balanced rutile alumina-silicate flux coating that deposits duplex weld metal containing some 40% delta ferrite and 60% austenite. The flux is extruded onto a fully alloyed 29Cr-9Ni core wire using a blend of silicates that ensures both coating strength and resistance to subsequent moisture absorption.
WELDING FEATURES OF THE ELECTRODE
This unique flux formulation ensures excellent arc stability, ease of initial arc strike and re-strike, minimal spatter on AC and virtually none on DC+. The resultant weld seams are smooth, evenly rippled and free from undercut while slag detachability is excellent. Metal recovery is some 103% with respect to core wire weight.
For all-positional welding ideally use smaller diameters.
APPLICATIONS AND MATERIALS TO BE WELDED
Primarily designed for high carbon steels, cast or wrought, which are well known as difficult to weld or problem steels. The duplex microstructure of the weld metal will tolerate high dilution with such steels while still maintaining its strength ductility and thus resistance to cracking. It can also be used very successfully for joining carbon steels to stainless steels, the only exception to its extensive use on such applications is that at service temperatures above 300 ºC a drop in weld metal ductility occurs
WELDING AMPERAGE AC and DC
OTHER DATA
Electrodes that have become damp should be re-dried at 120oC for 30 minutes.